Por Ibon Linacisoro/Interempresas.-
Hermle protagoniza un taller en el que solo existen centros de cinco ejes
Ubicada en la localidad alavesa de Laguardia, allá donde los viñedos permiten un espacio a una zona de pabellones industriales, Riojacam se dedica al mecanizado de alto valor de piezas para numerosos sectores, con el aeronáutico como estrella principal. Convencido de que solo la tecnología elevada, la flexibilidad y capacidad de reacción le permitirá un futuro sólido, Miguel Álvarez, CEO de la empresa, explica en este reportaje su apuesta por los cinco ejes y las máquinas de primer nivel, como Hermle (representada en España por Delteco), entre otras.
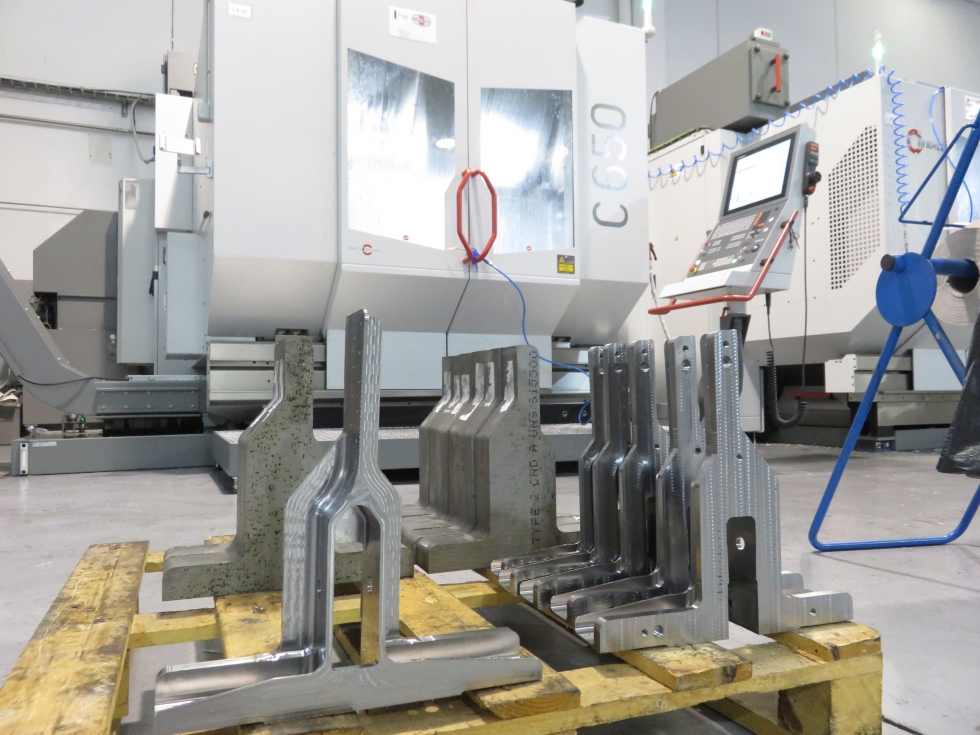
Visitar empresas que tienen centros de mecanizado Hermle suele tener algo en común: el convencimiento de sus responsables de que la batalla está en la dificultad, el valor elevado, el conocimiento y la experiencia. Tras años trabajando en el mundo del mecanizado para el sector de packaging, Miguel Álvarez fundó Riojacam en 2006 para dedicarse a la fabricación de piezas para máquinas destinadas al packaging, subcontratación en general, moldes, matricería etc.
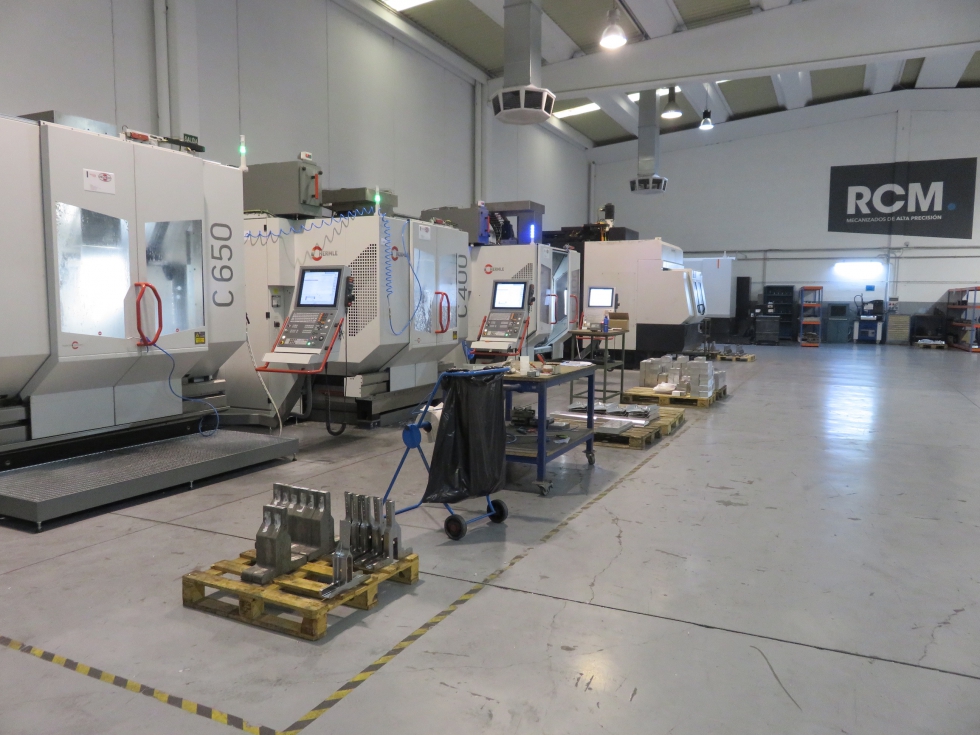
El descenso del trabajo y la crisis del sector de los moldes de los años 2009 y 2010, cuando numerosas empresas decidieron comprar sus moldes en China, fueron el detonante para dar un giro a la empresa. “Trabajando solamente para empresas de la zona y en sectores en crisis, decidí buscar otros nichos y me decanté por el sector aeronáutico. Hoy en día el sector aeronáutico representa el 70% de nuestra facturación y el resto corresponde al packaging, principalmente troqueles de precisión, y a la subcontratación de piezas con mucho valor añadido”.
Las piezas de aeronáutica que se mecanizan en Riojacam son, en su mayor parte, estructurales, aunque ya se están dando los primeros pasos en piezas de motor, especialmente para Boing. “Hemos optado por este camino -continúa el CEO de la empresa- porque en el aluminio hay mucha competencia. Estamos desarrollándonos para mecanizar materiales complicados como titanio, inconel, etc. y de hecho ya estamos mecanizando piezas de inconel 625 y 718. Contamos para ello con el equipamiento adecuado y tenemos el conocimiento necesario, porque hemos ido abriendo nuestro camino con esfuerzo e inversión. Estamos convencidos de que este es nuestro camino, porque en este segmento no hay tanta empresa preparada como la nuestra. Hay que tener en cuenta que la competencia, hoy en día, no la tenemos en las empresas de la zona, sino en todo el mundo. La clave es tener un equipo de profesionales con mucha experiencia y conocimiento, así como equipos que estén a la altura de las exigencias”. Claro que trabajar para el sector aeronáutico tampoco es garantía de estabilidad. Así por ejemplo, el anuncio de la retirada de la producción del Airbus 380 obligó a devolver una gran cantidad de material con el que ya se contaba para ese avión.
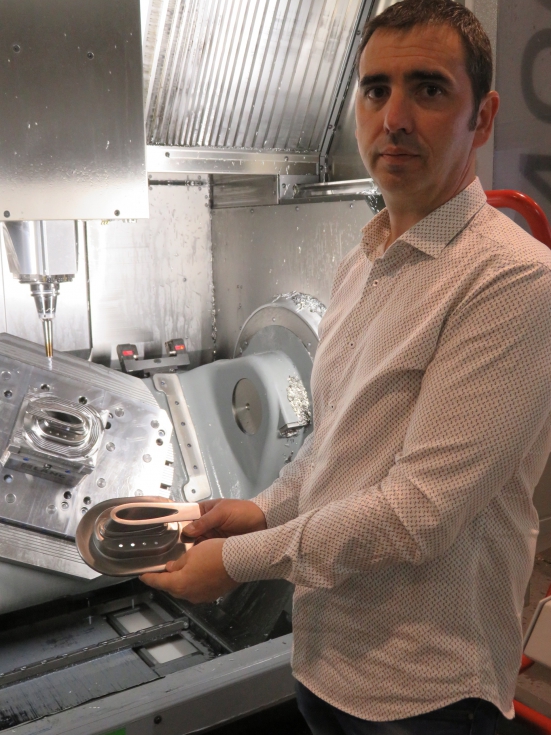
Un total de 24 personas trabajan en Riojacam, todas ellas bien cualificadas y preparadas para operar equipos avanzados. Tres de ellas se encargan de la oficina técnica y cuatro (de las cuales 3 son ingenieros) de calidad, documentación y verificación. Efectivamente, la documentación y calidad en aeronáutica requieren mucha dedicación, ya no solo para obtener las certificaciones, sino también para mantenerlas. Gracias a la apuesta por estos departamentos el ratio facturación / persona se ha elevado considerablemente.
Equipamiento avanzado
Las tolerancias estrictas con las que opera esta empresa alavesa se encuentran en el entorno de las centésimas. Una máquina de medir tridimensional y un brazo Romer, que funcionan a dos turnos, se encargan de este trabajo ineludible cuando se trata de suministrar al sector aeronáutico. “Cuando comenzamos nuestra actividad en aeronáutica no teníamos máquina tridimensional y no éramos conscientes de su relevancia. Ya no solo por cuestiones económicas, ya que los costes de una no conformidad son enormes, sino también por la confianza que generamos en el cliente, contar con una tridimensional de última generación, así como todo el departamento de calidad, es a día de hoy indispensable”.
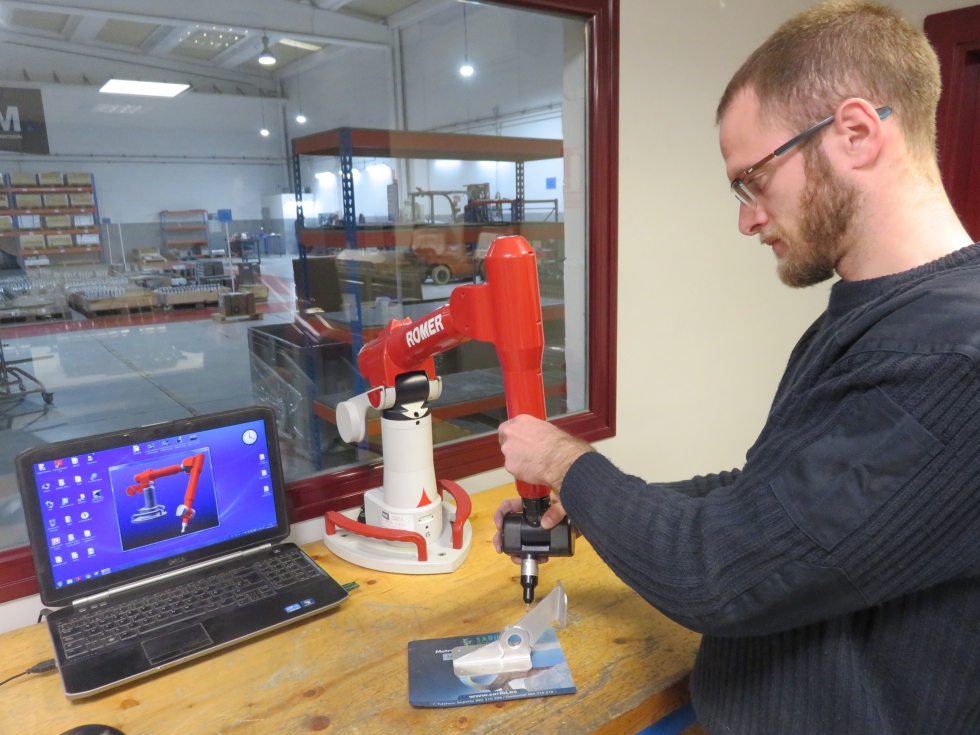
En lo relativo a los equipos de arranque de viruta, Riojacam ha seguido una evolución. En 2011 todas sus máquinas eran de tres ejes y fue precisamente ese año cuando incorporaron la primera de 5 ejes. Poco a poco fueron aprendiendo que los centros de mecanizado de cinco ejes no solo aportan ventajas en piezas de cinco ejes, sino también en las de tres: más rapidez, menos fallos, menos riesgos al cambiar piezas y de centrar… “Nuestra estrategia ahora mismo es que la pieza entre en bruto y salga terminada, sin cambiar la posición de la pieza. Hacemos todo lo posible para evitar tener que sacarla y volverla a amarrar. Cuantas más vueltas dé una pieza por el taller, más dinero vamos perdiendo. Para nosotros fue importante darnos cuenta de esto, porque realmente no son muchas las piezas de cinco ejes en continuo que existen. Recurrir a centros de cinco ejes para piezas de tres fue un paso muy importante y ahora mismo no creo que volvamos a comprar ninguno de tres ejes”.
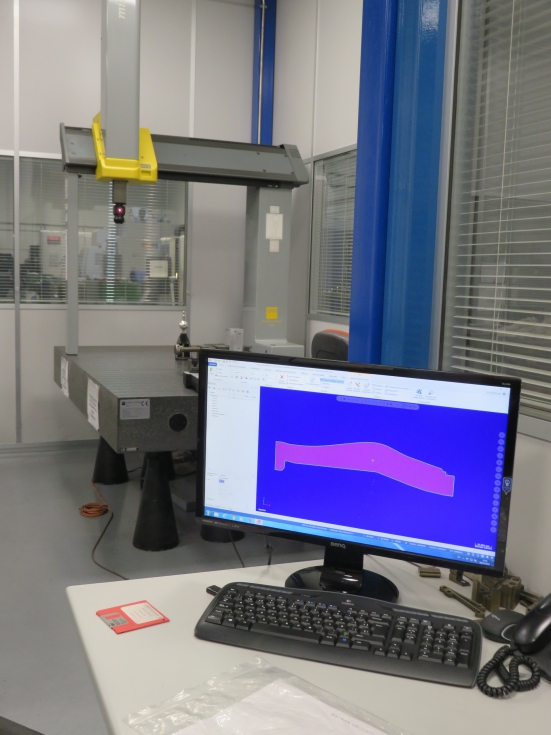
Claro que no todo es tan sencillo como simplemente proponérselo. También hay que tener en cuenta que una máquina de cinco ejes tiene que ir acompañada de buenos recursos de programación, portaherramientas y herramientas de primera calidad… Es un cambio de concepto por el que Riojacam decidió apostar, especialmente tras adquirir su primera Hermle de cinco ejes.
De hecho, sus diez centros de mecanizado son de cinco ejes, de las cuales cuatro son de Hermle.
Además de las máquinas de otras marcas, como Mazak o DMG, en su taller de mecanizado cuenta con una Hermle C400, dos C400 ZM50 y una C650.
Una muestra de cómo quedaron convencidos de todo ello en Riojacam es que, una vez probada la primera Hermle, las otras tres se compraron a lo largo de un solo año, en 2018. “La carga de trabajo que tenemos ahora hubiese sido inasumible con las máquinas que teníamos antes -explica Miguel Álvarez-. Además, esto ocurrió de forma paralela a la reducción del número de operarios en producción. En la actualidad, dos operarios y el responsable de turno llevan todo el taller. Lo de un operario – una máquina, ha pasado a la historia”.
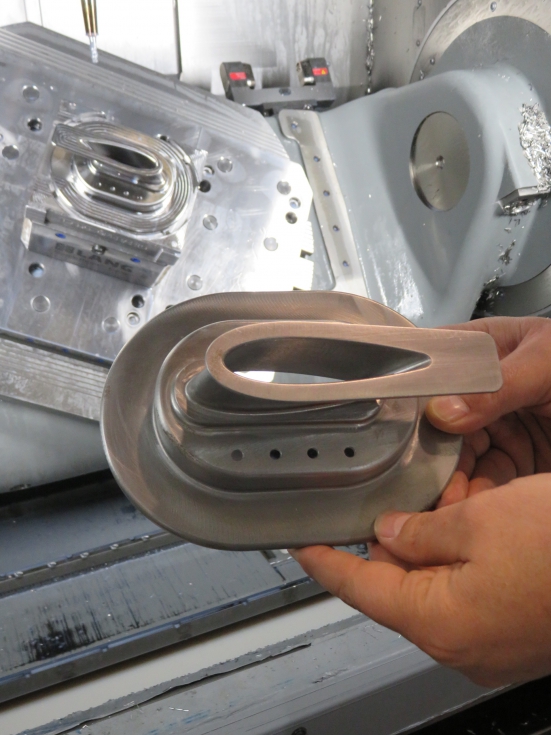
Tras asimilar las capacidades de las máquinas Hermle y el actual aprendizaje en el mecanizado de inconel, el siguiente paso será trabajar con más herramientas en la máquina y, posteriormente, progresar en la automatización. Es su propio avance en tecnología el que ha llevado a Riojacam a la necesidad de automatizar más la producción. Su CEO lo explica así: “Hoy en día los lotes de fabricación son mucho más reducidos que antes. Gracias a la tecnología de mecanizado con la que contamos, podemos hacer una pieza con mucha más rapidez, lo cual nos lleva a una situación que debemos resolver: mecanizamos muy rápido pero, dado que los lotes son pequeños, tardamos mucho en preparar la máquina para la siguiente pieza. En definitiva, habíamos avanzado mucho en oficina técnica, pero la máquina tenia muchos tiempos muertos. Lo hemos resuelto con una semiautomatización: preparamos en oficina técnica las piezas con los mismos sistemas de amarre y equipamos la máquina con las herramientas que va a necesitar. De esta forma hemos logrado que casi nos dé igual que el lote sea de tres o de diez unidades. Lógicamente esto requiere un trabajo previo exhaustivo para evitar cambios en la máquina. Hemos adecuado la oficina a lo que tenemos en taller. Todos estos avances nos han permitido tener más personal en calidad y oficina técnica. El resultado es un importante incremento de la producción y, sobre todo, de la productividad”.
Exigencia de un buen servicio
Una vez que Riojacam apostó por la estrategia de la alta calidad, la productividad y el alto valor, sus exigencias con los proveedores fueron progresando paralelamente. Efectivamente, el servicio del proveedor de las máquinas es fundamental. En ese sentido, Miguel Álvarez decidió continuar con Hermle, en buena medida por el servicio que le prestan desde Delteco, el distribuidor de estas máquinas alemanas en España. “Si la calidad en las máquinas ya de da por supuesta -afirma Miguel Álvarez- el hecho diferencial es el servicio postventa. No podemos estar parados esperando a que venga un componente de la máquina o que venga el técnico. Nosotros trabajamos en tres turnos y, en fines de semana, dos turnos. Es decir, una máquina parada es un problema muy importante, no solo económico sino en planificación y en la imagen ante nuestro cliente. Nuestro proveedor de máquina nos tiene que dar una solución con la máxima rapidez, porque si no, nuestro cliente nos penaliza o nos quita un paquete de trabajo. Tal y como producimos nosotros, el tiempo que perdemos ya no es recuperable, por el sistema de turnos que tenemos. Con Delteco el servicio es en 24 horas (Maximo 48 horas) y, sobre todo, vemos que están con nosotros, que se preocupan y sienten el problema como suyo, en definitiva, profesionales”.
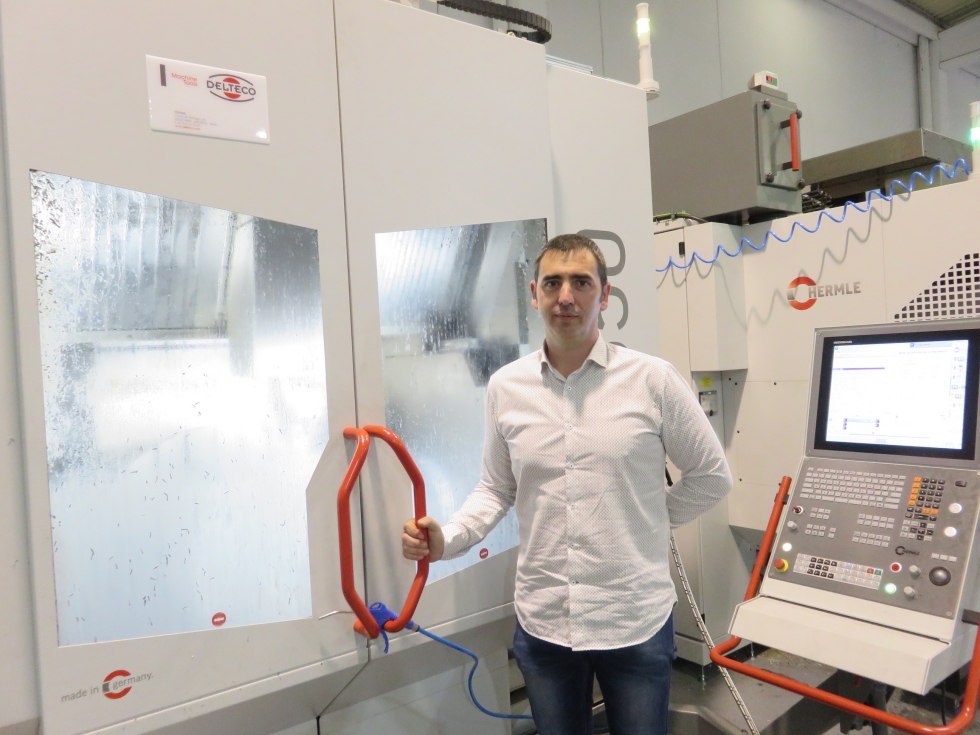
Como dato interesante y que explica lo anterior, Delteco cuenta con más de 30 técnicos, algunos de ellos especializados en Hermle. Es sin duda uno de los motivos por los que, especialmente en los dos últimos años, la presencia de máquinas Hermle en el mercado español ha crecido notablemente.
Riojacam con la Industria 4.0
Otro ejemplo de la voluntad de esta empresa por estar en la primera línea de la tecnología es su apuesta por sistemas que se enmarcan en el concepto Industria 4.0. En este sentido, ha
implementado un sistema de captura digital de datos en planta directamente sobre los centros de mecanizado. Esto permite conocer el OEE real, así como la productividad, incidencias, etc. en tiempo real.
Disponer de datos, en tiempo real, de todo lo que sucede en planta permite tomar las decisiones adecuadas en cada momento, sin necesidad de tomar estas decisiones con posterioridad, evitando así retrasos, perdida de agilidad, etc.
El CEO de Riojacam pone un ejemplo para explicarlo: “Por ejemplo, si una máquina está parada durante un tiempo superior al que nosotros hemos determinado previamente, salta una alarma en el sistema. Esta alarma nos permite seguir trabajando, pero obliga al operario correspondiente a introducir en el sistema cuál ha sido el problema. Aunque esté solucionada, la incidencia queda registrada y cuando observamos los informes, algo que hacemos cada día, sabemos cuál ha sido la causa de esa parada y podemos trabajar sobre ella”.
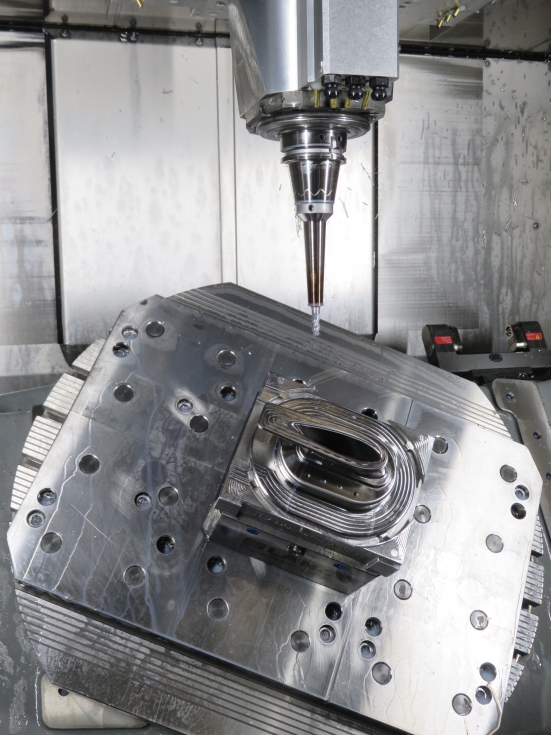
La captura digital de datos también permite eliminar progresivamente el papel en planta, ya que todos los datos introducidos en los terminales de los centros de mecanizado proporcionan toda la información necesaria en lo relativo a los costes.
El 70% de los equipos están actualmente operando con este sistema y a finales de año esta previsto implementar el 100%.
Para esta empresa el sistema implantado no solo está siendo importante desde un punto de vista operativo, sino también porque supone el principio de un camino con muchas posibilidades: “Lo que ya tenemos implantado nos ha hecho reflexionar sobre la relevancia de esta información real, y, más importante aún, la relevancia de saber tratar esta información. Requiere de un estudio de los datos para tomar las decisiones adecuadas en cada momento”.





