- Con el agarre inteligente, los grippers de SCHUNK miden, identifican y supervisan los componentes, así como el proceso de producción.
- El análisis de datos ayuda a detectar daños incipientes y garantizan un mayor control de calidad en todas las etapas
Hay una enorme cantidad de datos que están siendo producidos por las máquinas, sistemas automatizados y otras herramientas inteligentes que se encuentran en las fábricas de las empresas manufactureras. Sin embargo, se calcula que sólo un 5% de toda esta información se usa para algún fin, la mayoría en caso de daños o para la resolución de problemas. SCHUNK, referente mundial de sistemas de agarre y técnicas de sujeción, da un paso adelante hacia la producción inteligente aprovechando estos valores registrados en tiempo real para obtener un ahorro de costes, una mayor eficiencia operativa y una mejor calidad del producto.
La calidad de los datos importa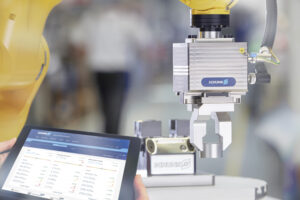
No sólo se trata de leer y enviar datos a la nube, a riesgo de colapsar el sistema, sino de analizarlos en tiempo real y convertirlos en información valiosa. El objetivo principal es perfeccionar los macrodatos y convertirlos en datos inteligentes para que se activen las respuestas adecuadas. Esto reduce el volumen de datos a transferir a lo que realmente se necesita, es decir, se transmiten indicadores clave de rendimiento (KPI). Por ejemplo, es necesario preparar información sobre si un sistema automatizado está funcionando correctamente y si se le han aplicado las medidas recomendadas adecuadas. De esta manera, se comprueban las características de calidad de los componentes durante la manipulación, así como tomar decisiones OK/NOK directamente en la pinza. Más importante es, si cabe, la determinación continua en tiempo real de la capacidad del proceso a largo plazo (Cpk) para la detección proactiva de tendencias y el diagnóstico de errores para obtener un historial de resultados con la pinza.
En el futuro, SCHUNK tiene previsto automatizar las tareas de control de toda la cadena cinemática, compuesta por robots y pinzas, así como la supervisión de su función, sin tener que estar programada para cada uno de los pasos o tener que establecer umbrales y ajustarlos continuamente. El uso de métodos de inteligencia artificial (IA) y el uso de diferentes sensores serán cruciales para este tipo de agarre autónomo.
La pinza paralela EGL, control y calidad en tiempo real
La pinza paralela EGL de SCHUNK ofrece un módulo de agarre estándar inteligente que incluye funciones integradas de serie, una interfaz Profinet certificada y un sistema electrónico integrado con carrera variable y una fuerza de agarre que puede ajustarse entre 50 N y 600 N. Como sistema de medición en línea, al “agarrar de forma inteligente”, la pinza inteligente utiliza su posición expuesta directamente en la pieza para obtener datos y evaluarlos inmediatamente mediante la tecnología punta integrada. Cada uno de los pasos del proceso puede ser controlado al detalle y, por ejemplo, transmitido al sistema de control, al sistema ERP de nivel superior y a las bases de datos de análisis y soluciones en la nube. De esta manera, el gripper inteligente es capaz de registrar y procesar sistemáticamente información sobre la pieza agarrada, el proceso y los componentes, y también de ejecutar las reacciones adecuadas. Esto nos permite obtener un control de calidad completo y supervisar directamente el proceso de producción en el ciclo de producción.
El portaherramientas inteligente iTENDO
Equipado con un sensor, una batería y una unidad transmisora, el portaherramientas iTENDO de SCHUNK supervisa el proceso a 5000 Hz en la herramienta. Un algoritmo calcula de forma continua un parámetro para la estabilidad del proceso. El valor IFT se ha desarrollado especialmente para este portaherramientas, y expresa la vibración medida en forma de valor numérico dentro de una escala definida de intensidad, similar a la escala de Richter para los terremotos. Si el corte se vuelve inestable, la inteligencia integrada interviene directamente en tiempo real con una latencia de aproximadamente 20 ms y sin intervención del operador. Dependiendo de la situación, el proceso se detiene, se reduce o se adapta a los parámetros básicos previamente definidos, se cambia la entrada de las herramientas, se sustituyen las herramientas o se envían mensajes al operador.
Dependiendo de la aplicación en particular, se puede usar un servicio web para definir los límites exactos y las reacciones correspondientes si se superan. A medio plazo, también ha de ser posible realizar evaluaciones estadísticas como la eficacia global del equipo (OEE), la capacidad del proceso (Cpk), el tiempo medio entre fallos (MTBF), o el desarrollo de tendencias como la desviación de los parámetros o los gradientes de las tasas de error.





