Lentes, espejos, tecnología de semiconductores, láseres, prototipos…
Para muchos componentes ópticos, como lentes o espejos, los requisitos para la precisión de los contornos y la calidad de las superficies son hasta una potencia de diez más estricta que para otros procesos de micro producción. Se requieren fracciones de un micrómetro o valores de rugosidad superficial en el rango nanométrico de un solo dígito. Además, las geometrías no lineales y, a veces, incluso las superficies de forma libre suelen estar involucradas.
Para tales tareas, una empresa especializada en ingeniería y servicios relevantes confía en un centro de mecanizado de fresado de cinco ejes con un husillo de alta frecuencia de cojinetes de aire.
«Nos hemos especializado en el mecanizado de ultra precisión de metales y plásticos», explica el Dr.-Ing. Olaf Dambon, director general de son-x GmbH en Aquisgrán (Alemania). Son-X fue fundada en 2011 como una escisión del Instituto Fraunhofer de Tecnología de Producción IPT, con sede en Aquisgrán, y hasta ahora ha experimentado un rápido crecimiento. La chispa inicial fue el desarrollo de un actuador que hace que un filo de corte hecho de un solo cristal de diamante vibre a frecuencia ultrasónica. Este filo de corte se utiliza como herramienta de torneado en torneado de ultra precisión con cojinetes de aire.
Gracias a la vibración, el tiempo de contacto del filo de corte con la pieza de trabajo es extremadamente corto durante cada ciclo, suprimiendo así de manera eficiente las reacciones térmicas o químicas entre el filo de corte y la pieza de trabajo.
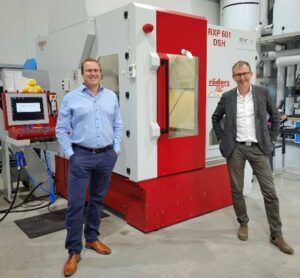
Esto hace posible utilizar el filo de corte de diamante incluso cuando se mecaniza acero. Las aplicaciones incluyen insertos de molde para producir lentes por moldeo por inyección. El sistema «UTS2», que consiste en un generador ultrasónico y un portaherramientas, fue desarrollado para su uso en los cordones de precisión. Los husillos ultrasónicos también se incluyen en la gama como una familia de productos adicional.
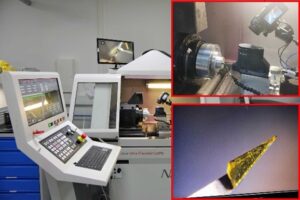
Proveedor de servicios de ingeniería y mecanizado de precisión
«Sin embargo, el uso óptimo de estas soluciones también requiere una gran cantidad de conocimientos, por lo que la mayoría de los clientes prefieren comprar componentes o prototipos terminados «, agrega el Director General Dr.-Ing. Benjamín Bulla. Con este fin, además de la amplia experiencia en ingeniería en el mecanizado de alta precisión de componentes, también se han construido las capacidades de fabricación correspondientes.
Son-X fabrica componentes metálicos hechos de varias aleaciones, incluidos aceros de alta resistencia, así como piezas hechas de plásticos, en su mayoría cristalinos.
Las cantidades van desde piezas individuales hasta varios cientos por año, las dimensiones se extienden desde unos pocos mm hasta diámetros de 500 mm, por ejemplo, en el caso de los espejos metálicos. Las aplicaciones incluyen óptica, tecnología láser, tecnología de sensores y astronomía, así como moldes para sistemas de guía de luz e iluminación para la industria automotriz. Además, pueden abarcar la producción de matrices ópticas, así como proyectos de investigación pura, como la fabricación de espejos para la instalación Wendelstein-7-X para experimentos de fusión nuclear en el Instituto Max Planck en Greifswald.
Incursión en el fresado de 5 ejes
«Con el tiempo, comenzamos a recibir más y más solicitudes de piezas cuya geometría era demasiado compleja para ser producidas por torneado», recuerda el Dr. Dambon. Para encontrar una máquina adecuada para este propósito, se elaboró una hoja de especificaciones y se diseñó una geometría de prueba. Luego comenzó el proceso de identificación de posibles proveedores. El contacto con Röders se estableció en 2016 en la feria Optatec, donde la compañía había mostrado insertos de molde mecanizado de alta calidad, entre otros artículos. Además de Röders, otros cuatro fabricantes de máquinas activos en el campo del mecanizado de alta precisión fueron preseleccionados, incluidos tres fabricantes japoneses. Después de intensas discusiones preliminares, los candidatos finalmente fueron provistos de los datos CAD para un componente de prueba que exhibió los desafíos más significativos de las tareas previstas. En esta comparación, la pieza de prueba mecanizada por Röders tuvo el mejor desempeño. Dado que la consulta inicial también había sido convincente, el fabricante de máquinas con sede en Soltau se adjudicó el contrato para un centro de mecanizado de fresado de 5 ejes del tipo RXP 601 DSH.
Características especiales del Röders RXP 601 DSH
El centro Röders RXP 601 DSH HSC de 5 ejes ha sido diseñada para cumplir con los requisitos de precisión más altos y, al mismo tiempo, proporcionar altas tasas de eliminación de metales, especialmente cuando se mecanizan materiales duros. Cuenta con accionamientos directos lineales sin fricción que, en combinación con controladores de 32 kHz en todos los ejes, permiten un mecanizado altamente dinámico y de alta precisión.
Un requisito previo esencial para esto son las reglas ópticas de alta precisión en todos los ejes: cuando se trata de precisión, no se hacen concesiones. Debido a su precisión y dinámica, la máquina también se puede utilizar para el rectificado de coordenadas. Además, el eje Z cuenta con una compensación de peso de vacío patentada sin fricción.
Para garantizar la máxima estabilidad térmica, la máquina cuenta con un sofisticado sistema de gestión de temperatura. La temperatura del medio que fluye a través de todos los componentes principales del sistema se controla con una precisión de ± 0,1 K, o ± 0,02 K para ciertas aplicaciones. Otra característica especial es un sistema de control dedicado basado en tecnología de PC, cuyas funcionalidades se adaptan con precisión a las tareas específicas de fresado de alta precisión HSC o rectificado por coordenadas. Dado que Röders ha desarrollado el propio sistema de control basado en PC industriales y el sistema operativo Windows, las actualizaciones tanto del hardware como del software están disponibles bajo petición en cualquier momento, por lo que la obsolescencia de las máquinas por parte de su sistema de control es prácticamente imposible. En la versión actual del sistema de control con la función Racecut, la corrección de las desviaciones de trayectoria tiene lugar con la frecuencia de muestreo excepcionalmente alta de 32 kHz en cada bucle de control. Esto permite reducciones significativas en el tiempo de mecanizado y, al mismo tiempo, garantiza una calidad óptima de la superficie.
«En vista de nuestros requisitos de precisión, los factores de rigidez, funcionamiento suave y estabilidad térmica fueron altos en la lista de prioridades «, dice el Dr. Bulla. En comparación con la minuciosidad de los detalles a mecanizar y las micro herramientas utilizadas para este propósito, la fresadora Röders, que también es adecuada para las operaciones de desbabado más duras, parece bastante sobredimensionada a primera vista.
Sin embargo, fue precisamente esta masa y las medidas tomadas por el fabricante para garantizar la mayor precisión de los resultados de mecanizado lo que tuvo un efecto excepcionalmente positivo en este caso. Al mecanizar matrices ópticas complejas con cientos de pequeñas cavidades para lentes, un trabajo a veces toma más de 50 horas, y durante todo este tiempo, el punto de referencia de la máquina debe permanecer extremadamente estable para garantizar la alineación exacta de cada lente. El RXP 601 DSH logra esto, dice, gracias a sus accionamientos directos lineales, guías lineales de alta precisión y compensación de peso sin fricción para el eje Z, combinados con reglas ópticas de alta precisión. Con su funcionalidad Racecut de gama alta, el sistema de control compara las posiciones reales y objetivo de todos los ejes 32.000 veces por segundo, corrigiendo incluso las desviaciones de trayectoria más mínimas a medida que ocurren.
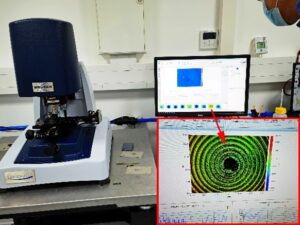
La estabilidad térmica excepcional es proporcionada por un medio de control de temperatura que circula a través de todos los componentes importantes del sistema y cuya temperatura de suministro se mantiene constante con una precisión de ±0.02K. Por supuesto, la temperatura de la sala en la que se encuentra la planta también se mantiene estable mediante un sistema de aire acondicionado. Finalmente, como guinda del pastel, la máquina está equipada con un husillo Levicron controlado por vectores cojines de aire con hasta 60,000 RPM. Gracias a su funcionamiento suave y alta amortiguación, este husillo permite producir superficies de primera calidad en todos los materiales. Como esto elimina la necesidad de reelaboración manual, también evita la distorsión relacionada y a menudo inevitable, de la superficie o la geometría. Otro requisito previo esencial para obtener los mejores resultados es la alta precisión de la planificación de la ruta de la máquina. En combinación con los programas NC calculados con la mayor precisión por un potente sistema CAM, la geometría CAD deseada se reproduce en la pieza de trabajo sin errores ni desgaste.
Experiencias experimentadas durante la entrega, familiarización y capacitación.
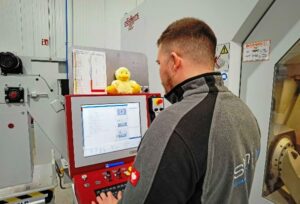
«El centro de mecanizado se entregó en octubre de 2018 y pudo ponerse en funcionamiento en solo una semana», informa el Dr. Dambon. El cursillo de cuatro días también fue con una suavidad similar. Los empleados se familiarizaron rápidamente con el nuevo sistema de control, ya que es muy intuitivo de operar.
El cambio del sistema de control de ® Heidenhain, con el que ya estaban familiarizados, fue agradablemente fácil. En este contexto, por supuesto, fue útil que el control de Röders también se pueda programar directamente con ciclos Heidenhain®. La transferencia de datos desde el software CAM utilizado en Son-X resultó ser fácilmente factible.
El asesoramiento y el apoyo durante la fase de aceleración fueron igualmente satisfactorios. Si a veces surgían problemas, la asistencia se prestaba rápidamente y con un alto nivel de competencia.
Solo hubo un mal funcionamiento en la máquina debido a un problema de interruptor, pero esto se diagnosticó y rectificó rápidamente con la ayuda del mantenimiento remoto. A lo largo de más de dos años de cooperación, Röders ha demostrado ser un socio confiable.
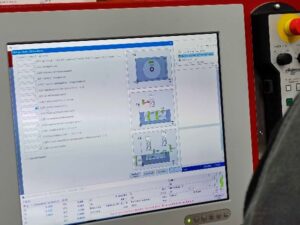
Altamente satisfecho con los resultados
«Dado que tenemos muchos trabajos de larga duración, la estabilidad a largo plazo del punto de referencia también es crucial para nosotros, además de la precisión que es posible en poco tiempo», revela el Dr. Bulla. Y sobre este punto dice, están realmente impresionados con el sistema Röders. Por ejemplo, tuvieron que mecanizar moldes para matrices de cientos de lentes de plástico cuya desviación de forma se permitió que fuera un máximo de 316 nm, es decir, 0.316μm (!). Este valor se mantuvo de manera confiable incluso después de 50 horas de uso, incluso para la última lente de la matriz. La compañía también se sorprendió gratamente por la velocidad de operación.
Mientras tanto, llegan tantos pedidos de piezas que la máquina se utiliza casi a tiempo completo. «Estamos muy satisfechos, los resultados esperados están ahí e incluso se han superado en algunos casos «, dice el Dr. Bulla, resumiendo su experiencia.
Más información:
✉ comercial@comher.com
📞 937 29 54 54
💻 www.comher.com





