El mecanizado duro por encima de 58 HRC reemplaza la electroerosión por penetración de troqueles
El rendimiento y la eficiencia de los accionamientos eléctricos dependen del espacio de aire más estrecho posible entre el rotor y el estator. La tendencia hacia los trenes motrices electrificados aumenta así las exigencias de precisión de las piezas estampadas requeridas para este fin. Por lo tanto, las especificaciones de tolerancia para las herramientas de conformado y estampado utilizadas para producir las piezas de chapa correspondientes son correspondientemente estrechas.
El rango de μm de un solo dígito medio a inferior se especifica cada vez más. Por lo tanto, ZF Tech Centre “Herramientas, equipos de medición y sistemas de automatización” en Schweinfurt está invirtiendo fuertemente en esta área. Entre otras cosas, la tendencia es pasar de la electroerosión por penetración al mecanizado HSC.
Se han logrado aumentos significativos en la vida útil de la herramienta mediante la optimización de la lubricación.
El mecanizado se lleva a cabo las 24 horas del día, los 7 días de la semana, en una línea de producción con cuatro centros de mecanizado HSC, cuatro máquinas de electroerosión por hilo, una máquina de electroerosión por penetración de troqueles complementada por una estación de limpieza y dos máquinas de medición por coordenadas.
Somos responsables del desarrollo y la producción de herramientas, equipos de medición y dispositivos de automatización para la división Electrified Powertrain Technology de ZF
Gerd Ringelmann, Senior Manager Electrified Powertrain Technology y Jefe de Producción de Tech Centre
El Grupo globalmente activo con alrededor de 150.000 empleados y una facturación de aproximadamente € 32 mil millones se ha convertido en uno de los principales actores internacionales en el campo de la movilidad eléctrica. En consecuencia, el departamento dirigido por Gerd Ringelmann se centra fuertemente en los accionamientos eléctricos. Entre otras cosas, produce herramientas, equipos de producción y medición para la fabricación de componentes para motores eléctricos. Al hacerlo, la compañía con sede en Schweinfurt se centra constantemente en las redes, la Industria 4.0 y la producción automatizada sincronizada. Por segunda vez en los últimos años, el Tech-Centre 2021 fue nombrado el ganador general de la competencia alemana de la industria “Excelencia en la Producción” (EIP) por el progreso que ha logrado. Por lo tanto, es considerada como la empresa líder en la fabricación de herramientas y troqueles en la región de habla alemana. Esta reconocida competencia anual ha sido organizada durante 18 años por el Laboratorio de Máquina Herramienta de la Universidad RWTH Aachen y el Instituto Fraunhofer de Tecnología de Producción (IPT).
Mecanizado en duro HSC, automatizado
Nuestra línea de producción de tecnología cruzada y totalmente automatizada para el mecanizado duro ciertamente jugó un papel importante en la decisión del jurado
Bernd Rudloff, jefe de mecanizado en el Tech-Center en Schweinfurt
La línea consta de dos segmentos, uno para mecanizado EDM y un segundo para fresado duro HSC. Los sistemas de ambos segmentos están alineados a lo largo de un riel lineal que soporta un sistema de manipulación que les suministra piezas de trabajo y herramientas.
El área de fresado de la línea comprende cuatro centros de mecanizado de fresado de Röders y una máquina de medición de coordenadas de Zeiss. Dos de los sistemas Röders tienen tres ejes, mientras que los otros dos tienen cinco ejes. La programación se realiza utilizando el software Power Mill CAM de Autodesk, con programadores que también operan las máquinas.
Una nueva era de filosofía de mecanizado
“En esta línea, el 95 por ciento de las piezas de trabajo se endurecen hasta 65-67 HRC”, dice Gerd Ringelmann. En algunos casos, incluso se mecanizan carburos de tungsteno o cerámicas. Esto se ha hecho factible gracias al enorme aumento en el rendimiento de las herramientas de fresado en los últimos años en combinación con la integración de un nuevo sistema de enfriamiento de herramientas.
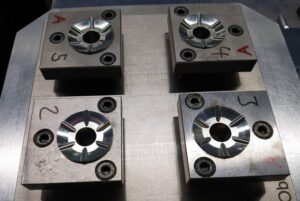
Por lo tanto, la empresa ahora puede omitir el enfoque de mecanizado anterior de dos etapas con endurecimiento intermedio en favor del mecanizado de una sola etapa en el estado endurecido. Además del tiempo de rendimiento reducido, las piezas de trabajo ahora también se pueden producir a un costo menor. Las tasas de eliminación de metal más altas también suelen hacer posible prescindir de la electroerosión por penetración y producir las geometrías deseadas directamente mediante fresado o rectificado. Por lo tanto, la línea de electroerosión ascendente cuenta con un solo sistema de electroerosión por penetración de troqueles.
Sofisticada tecnología patentada de lubricación por refrigeración por aire
“En el fresado duro, el suministro de lubricantes refrigerantes al área de corte juega un papel decisivo“, sabe Bernd Rudloff. Por lo tanto, se invirtió un gran esfuerzo en aclarar estas interdependencias. Esto incluso se convirtió en el foco de una tesis de diploma. Además del mecanizado en seco, la refrigeración con aire comprimido y la conocida lubricación de cantidad mínima mediante dos chorros de componentes, también se investigó la solución defendida por Röders, el suministro de un lubricante fino en aerosol con el distribuidor de medios de MHT. Esta tecnología utiliza un manguito de doble pared adaptado a la geometría de la herramienta con boquillas dispuestas hacia abajo, suministrando aire y lubricante a todos los bordes de corte de la herramienta de manera uniforme durante todo el proceso y, al mismo tiempo, asegurando la eliminación de virutas.
El manguito no gira con la herramienta, sino que se brida al eje Z a través de un adaptador y se suministra con aire comprimido aerosolizado con un lubricante a base de hidrocarburos. La herramienta y la funda se almacenan juntas en el cargador de herramientas y se intercambian juntas como una unidad. Para las pruebas, la empresa Weschu, como representante del área de Röders, proporcionó una máquina de demostración especialmente equipada con el distribuidor de medios MHT.
Las pruebas de mecanizado se realizaron utilizando piezas de dos aceros (X50CRMoV8-2 con 59+1 HRC y X230VCr8-5-4 Vanadis 8 con 62+2 HRC) sobre una Röders RXP 601 DSH. Para el mecanizado se utilizaron velocidades de avance de hasta 3.000 mm/min y velocidades de husillo de hasta 40.000 rpm. Se utilizaron herramientas de fresado de carburo sólido toroidal y de extremo de bola para las pruebas de desbaste y acabado.
La valoración electrónica de los resultados de la prueba se realizó de acuerdo con una serie de criterios, como el desgaste de la herramienta y la vida útil de la herramienta o la calidad de la superficie de las piezas de prueba. En todas las categorías, la solución MHT funcionó mejor, en algunos casos por un margen considerable.
Para las tiradas de acabado, se lograron aumentos de la vida útil de la herramienta del 50%. En el caso del desbaste, además del mismo aumento en la vida útil de la herramienta, el tiempo de mecanizado también se redujo a la mitad al aumentar la alimentación hacia adelante.
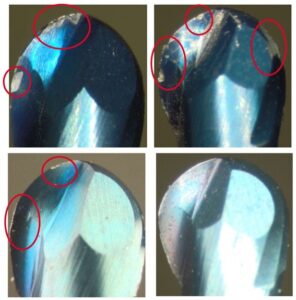
Con las otras tres variantes de proceso, duplicar la velocidad de avance resultó rápidamente en la rotura de la herramienta debido a la sobrecarga de los bordes de corte de la herramienta. En vista de estos resultados convincentes, el distribuidor de medios MHT fue seleccionado como el sistema superior y adaptado en todos los centros de mecanizado de Röders. La experiencia práctica después de la modernización confirmó las expectativas: se lograron ahorros del 13 por ciento en los costos de herramientas calculados sobre todas las piezas, así como aumentos en la producción del 10%. Además, hubo otras ventajas significativas como la sustitución parcial o completa de la electroerosión por fresado, una mejor limpieza -un factor que cada vez cobra más importancia, especialmente en procesos de fabricación altamente automatizados- y la eliminación del tratamiento de pulido debido a la buena calidad de la superficie. Están pendientes otras calificaciones, así como investigaciones centradas en el “fresado de alto brillo”.
Organización de fabricación
“En otra nota, también pudimos lograr avances decisivos en todo el Tech Centre con respecto a nuestra organización de producción”, dice Gerd Ringelmann con una sonrisa. Particularmente dignos de mención, dice, son la transición a la producción de flujo cronometrado y el manejo sin papel de todos los procesos.
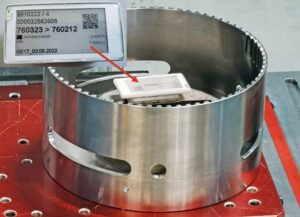
Un ciclo de reloj comprende un día: dentro de este período de tiempo, el carro con las piezas recibidas por un departamento debe procesarse completamente para estar disponible para la siguiente estación programada al día siguiente. El software de logística tiene en cuenta la disponibilidad de materiales y máquinas, así como la disponibilidad de los empleados a lo largo de toda la cadena de procesos. Todos los documentos relacionados con el trabajo se gestionan completamente dentro del sistema de TI y están disponibles en la estación de trabajo respectiva en una versión constantemente actualizada. Esta perfección es aún más importante porque el número promedio de piezas por trabajo es de solo 1.7, por lo que la mayoría de las piezas son artículos individuales, lo que prácticamente excluye cualquier asignación por errores o retrasos.
Asociación a largo plazo con Röders
“Nuestra decisión a favor de Röders para la adquisición de las fresadoras para la línea de mecanizado en duro se basó no solo en el rendimiento de los sistemas, sino también en muchos años de buena experiencia con el fabricante”, recuerda Bernd Rudloff. El primer sistema Röders se instaló en Schweinfurt hace más de 20 años. Desde entonces, su tecnología específica ha sido capaz de ganar puntos, especialmente en el campo del mecanizado duro, debido a su rendimiento de corte y la calidad de la superficie lograda en las piezas de trabajo, así como la precisión de las piezas que se pueden producir. El asesoramiento y el apoyo de Röders durante la introducción del distribuidor de refrigerante MHT también fueron convincentes. El compromiso personal de Herbert Merz, Director General de MHT, también hizo una importante contribución a su uso eficiente. Para explotar todo el potencial de la tecnología MHT, la estrategia CAM y los parámetros de procesamiento también tuvieron que adaptarse a las capacidades ampliadas.
Otro aspecto convincente es el concepto de control de las fresadoras Röders, que se basa en dos PC industriales e impresionó por su facilidad de uso y la posibilidad de actualizar fácilmente el sistema de control. Otro punto a favor fue la robustez de las máquinas, que sobresalieron por su baja susceptibilidad a los incumplimientos y los largos intervalos de mantenimiento. La fresadora más antigua ahora integrada en la línea, una RHP 600, data de 2006 y aún impresiona por su excelente precisión. Los resultados también son convincentes en términos de vida útil del husillo. Originalmente, se había asumido una vida útil esperada de 3.000 horas en función de la experiencia con otras marcas. Actualmente, este valor se está desplazando más hacia las 10.000 horas de funcionamiento para los sistemas Röders.
Independientemente de los cuatro centros de mecanizado de fresado de la nueva línea de fresado, otros dos sistemas Röders se utilizan actualmente como máquinas independientes. Se utilizan para el rectificado por coordenadas y se caracterizan no solo por su alto rendimiento sino también por la buena calidad de las superficies que producen.
“En resumen, puedo decir que la empresa Röders ha demostrado su valía en más de 20 años a través de buenos productos, asesoramiento experto y un servicio eficiente. Además viene la participación como socio competente en proyectos de desarrollo conjunto”, resume Gerd Ringelmann.





